Initial/In-process/Final Product Management System
Product Overview
Real-time self-inspection monitoring and efficient management of data for Initial/In-process/Final product.
The MATE-Initial/In-process/Final Product Management System is a self-inspection management system that ensures data reliability and maintains a quality system through defect analysis. It facilitates sampling, measurement, review, verification, storage, and analysis of inspection data for initial, in-process, and final stages of production processes.
Initial/In-process/Final product management is a part of the self-inspection process during product manufacturing. Workers regularly check the product status at predetermined intervals (Initial/In-process/Final) in the production process. Self-inspection involves the worker conducting inspections of the products produced within their own manufacturing process. The worker inspects the product based on predefined inspection items, using designated tools, at set times, and records the measured values.
Need for Implementation
-
Worker omissions of inspection records
-
Batch entry of inspection records
-
Decreased data reliability
-
Loss of manually recorded data
-
Inability to sustain the quality management system
-
Failure to obtain ISO/TS/SQ certification
-
Inability to implement fundamental measures to prevent defects
-
Risk of LOT defects
-
Increased cost due to defect-related losses
-
Inability to identify the timing of defect occurrences
-
Inability to trace root causes of defects
-
Occurrence and leakage of large-scale defects
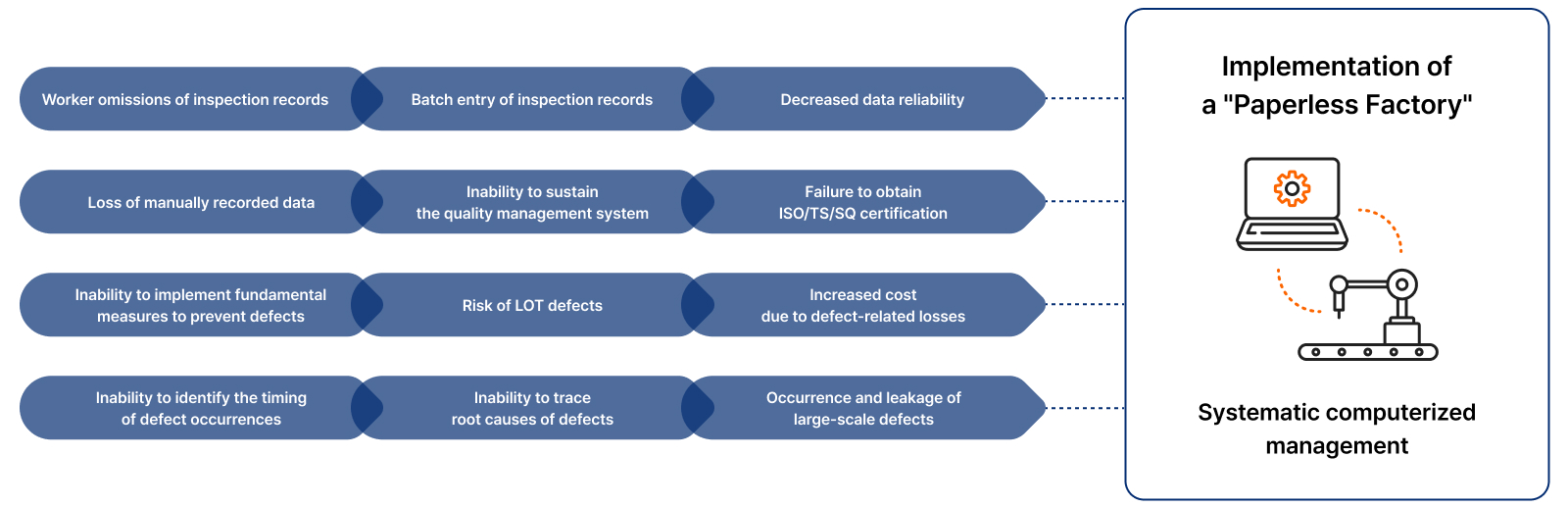
Core Functions
-
Entering Measurement Values into the System
Value Input Methods -
System-based storage Measurement values registered on devices are transmitted and stored in the system
Data History -
Real-time Monitoring Monitoring screen for
Initial/In-process/Final product management
inspection status
Implementation Case – Automotive Parts Manufacturer
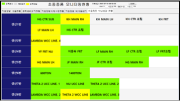
for Initial/In-process/Final product
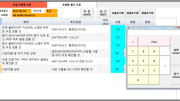
of data for each Initial/
In-process/Final product item
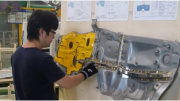
and final inspections
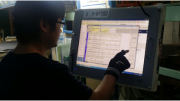
using devices
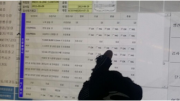
on devices (zoomed view)
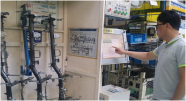
inspection data on devices
Expected Benefits
-
Strengthen management
Enhancement of basic quality control through improvement of Initial/In-process/Final product management methods
-
Statistical Process Control (SPC)
Possibility of utilizing statistical process control (SPC) through database-driven insights
-
traceability
Ensuring traceability of quality history through the database (DB) of measurement values
-
Prevention of omission
Prevention of inspection omissions and rapid response to process defects through real-time monitoring
-
Defect leakage prevention
Prevention of large-scale defects through interlocks (alarm/stop) in case of inspection omission or abnormal measurement values