MATE-MES(Manufacturing Execution System)
Product Overview
MATE-MES is a specialized Manufacturing Execution System (MES) solution developed by COMPUTERMATE Co., Ltd., leveraging the company’s accumulated expertise. This field support and management system reflects the realities and conditions of the manufacturing industry, enabling systematic management of planning and execution information on the production floor.
MATE-MES optimizes production activities occurring on the shop floor through a series of directives and management processes. This management support system facilitates rapid and seamless responses to dynamic shop floor conditions. Based on the 11 core functions of MES as defined by the American MESA, MATE-MES has been packaged and customized to address the specific needs of small and medium-sized enterprises (SMEs) and manufacturers.
Key Features
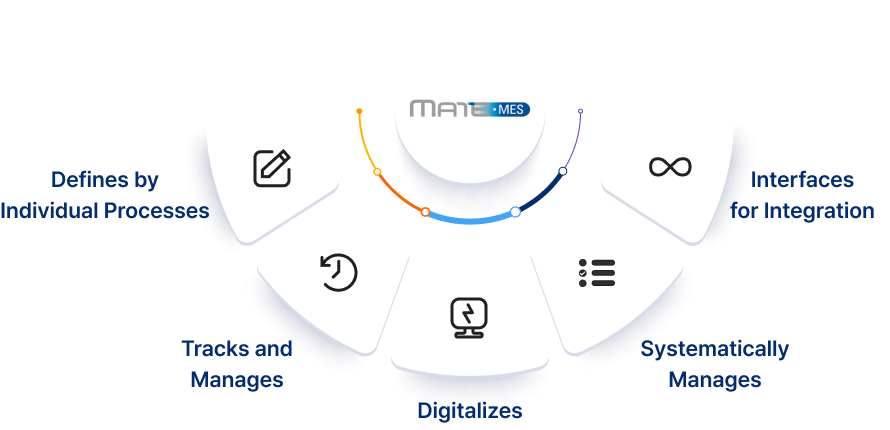
-
Defines by individual processes
Defines management elements such as equipment, materials, and operators by individual processes
-
Tracks and manages
Tracks and manages all materials according to predefined specifications
-
Digitalizes
Digitalizes detailed execution results and measurement data of products by each process
-
Systematically manages
Systematically manages all factory resources
-
Interfaces
for integrationProvides interfaces for integration with other systems
Necessity of Adoption
Evaluate your readiness for MES adoption using a self-diagnosis checklist:
-
Inadequate knowledge-based information systems for shop floor management
-
Lack of integrated functionality for production activities
-
Insufficient information sharing across factories, departments, processes, and workflows
-
Difficulty monitoring production progress at various stages
-
Discrepancies between raw material input and physical inventory
-
Limited ability to provide or collect critical on-site operational data
-
Inability to respond flexibly to sudden changes in production conditions
-
Challenges in gaining transparent visibility and making prompt decisions
-
Need for a comprehensive system to oversee shop floor operations and support decision-making
-
Difficulty addressing discrepancies between ERP production requirements and actual results
-
Managers spending 25–35% of their time verifying and correcting on-site data
Core Functions
-
MES is an integrated production management system.
MATE-MES integrates seamlessly with existing systems, such as ERP (Enterprise Resource Planning), to streamline material receipt and issuance using barcodes or other methods. It ensures clear traceability and enables quality control by handling each step—production planning, work orders, process management,
and performance recording—at the appropriate management unit.In terms of product receipt and shipment management, the system uses wireless and wired scanners or PDAs to automate tasks, collect and analyze on-site information, and ensure accurate data processing.
This facilitates rapid decision-making for both operators and managers. -
MES enables Quality Control and Informed Decision-Making
MES is a system that oversees the entire production cycle, from initiation based on product orders to the quality inspection of finished products. It serves as an integrated information system for the production site, collecting various data in real time—such as production performance, worker activities, equipment status, and product quality information—and performing aggregation, analysis, monitoring, and control of the production process. This enables the establishment of a high-quality, profit-oriented production system.
In other words, MES is designed to improve productivity and meet the increasing customer demands for enhanced product quality. It allows companies to accurately monitor and manage real-time production status on-site, reflecting the characteristics of the company’s industry and production site while considering necessary management aspects.
Expected Benefits
MATE-MES can optimally manage the production activities of the 4Ms that exist on the production floor—Man (workers), Method (production methods), Material (materials),
and Machine (production equipment)—by collecting real-time data through the information system.
-
Improvement
Improved quality through systematic production management
Increased factory operational efficiency through standardization of information within the factory
Accurate Root Cause Identification and Rapid Response Capability
-
Decrease
Reduction in cycle time and lead time
Reduction in documentation tasks between shift teams
Decrease in product defect rates
Reduction in Work-in-Progress (WIP)
-
Management
Real-time data collection and statistical process control through automation
Enhanced visibility of information, enabling consistent management by workers, managers, and top management
Real-time monitoring of WIP performance for equipment