MATE-POP
Product Overview
MATE-POP (Point of Production) is a standardized production point management system for manufacturing plants. It is a solution designed to eliminate many inefficiencies caused by the inability of many manufacturers to quickly and accurately collect production-related information.
By managing various production-related data in real time, it provides information that can be used for company management metrics, control, and sales information. Based on industry-specific templates, MATE-POP enables affordable system implementation and quick deployment, minimizing the customer's investment burden while maximizing the effectiveness of the system and reducing the risk of failure when applying the new system.
Key Features
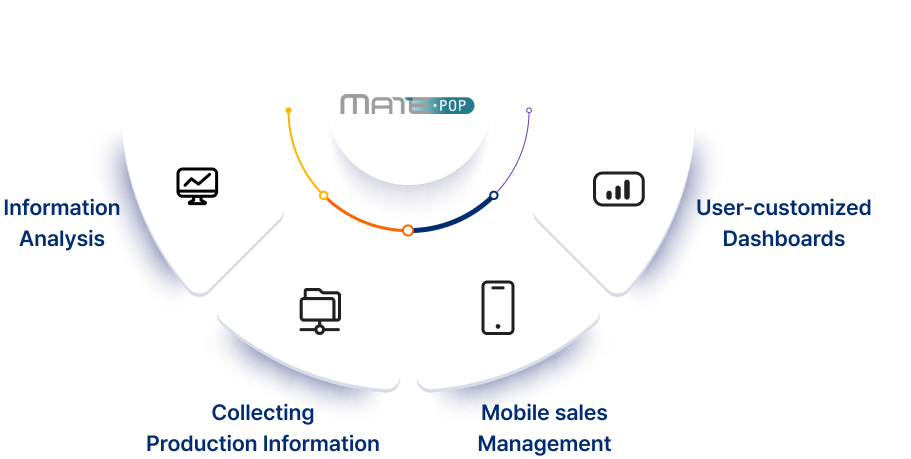
-
Information Analysis
Real-time collection, analysis, and monitoring of various information generated on the production floor.
-
Collecting Production Information
Production information can be collected in both semi-automatic and fully-automatic modes.
-
Mobile sales Management
Mobile sales management enables sales tasks to be handled anytime, anywhere.
-
User-customized Dashboards
User-customized dashboards provide a clear overview of production status and performance at a glance.
Necessity of Adoption
-
Existing systems are not functioning properly.
-
Challenges in managing production performance information.
-
Complications in registering defects.
-
Difficulty in monitoring the current progress of production.
-
Low reliability of cost management data.
Core Functions
-
Automatically receive production plan information
from upper-level systems by integrating with
existing information systems or ERP systems in operation,
and use it as production instruction information. -
Real-time integration of production performance,
quality information, and other data from the shop floor
into the upper-level systems (can be integrated with various
well-known ERP systems, both domestic and international).
-
Receive master data from upper-level systems to be utilized in MATE-POP,
and manage information not handled by the upper-level systems,
such as equipment codes, failure codes, and quality defect codes, independently. -
If the upper-level system is not set up or is incomplete, MATE-POP can independently
establish production plans and schedules, and input the necessary master data for system operation.
-
Provides real-time information on the production status of
the shop floor in various forms, including production results
and performance analysis against goals by product, process,
work order, and time period, which is often impossible in
most ERP systems.
-
Real-time analysis of various quality information generated
during production, including defect rates by product/resource,
analysis of the top 10 defects by product/resource,
share of total defects, rework/scrap occurrence data,
and defect trends by date/resource through graphical representation.
This enables effective quality management by monitoring and
analyzing quality issues as they arise in production.
-
By Providing analysis information through various types of graphs,
such as equipment failure status, management of the top 10 breakdowns,
equipment utilization rates, and trends in failures by type, this data serves
as the foundational material for establishing equipment maintenance plans. -
Real-time collection of breakdown and downtime information from the field
enables efficient equipment management.
-
To determine the efficient operation of production results
and the human resources invested in production activities,
it provides real-time analysis of vast amounts of information
through attendance management, labor input analysis, and
overall productivity analysis of on-site employees,
enabling managers to perform various forms of management.
-
Enhances the precision of LOT tracking for accurate
history management, allowing for forward and backward LOT tracking,
tracking of shipping data for the same LOT, and tracking
of the same material LOT.
-
A function for real-time viewing and monitoring of the production site's conditions.
-
A graphical interface designed to replicate the production line on a computer screen.
-
Connected to control devices like PLCs installed in the shop floor for information collection.
-
Enables real-time monitoring of production situations even outside the factory via
the internet through integration with domestic and international HMI (MMI) software.
-
Designed to provide an comprehensive overview of real-time monitoring
of the production site with monitoring screens replicating
the actual layout of the production facilities, along with detailed
monitoring screens for individual equipment.
It allows production managers and employees to monitor
the production status at a glance without needing to visit
the production site by desplaying information on materials,
sales, work-in-progress, inventory, and input/output details.
System Configuration
-
Example of Molding Management System Configuration
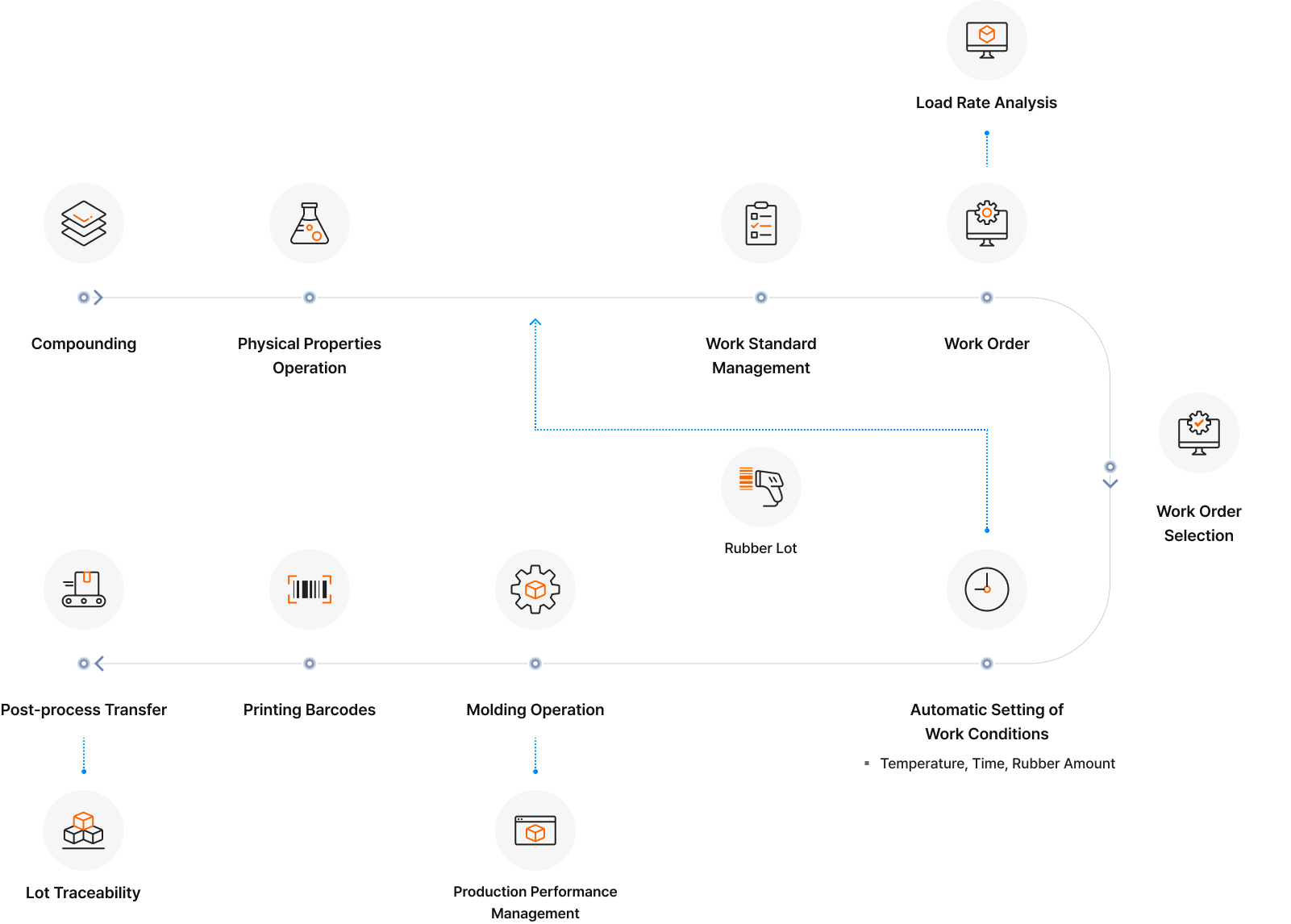
Expected Benefits
MATE-POP collects real-time data from the 4Ms present in the production field—Worker (MAN), Production Method (METHOD), Materials (MATERIAL), and Production Equipment (MACHINE)—through the information system, enabling optimal management.
-
Real-Time Field Monitoring
Manage equipment failures and downtime
Information on work delays and material shortages.
Minimize equipment idle time based on aggregated data per machine/operator/employee ID.
Secure production history to accumulate long-term plans and know-how.
Monitor work-in-progress (WIP) information in the production field.
-
Data Reliability
Ensures data reliability as production performance information is processed in real time.
-
Raw Material/Finished Product Management
Manage inventory, material flows, and outsourcing stock for raw materials and finished products.
-
LOT Traceability Management
Manages the entire process from raw materials to sales and customer shipment, including returns after shipment.
-
Customer Satisfaction
Improve customer satisfaction by reducing response time.
-
Identifying Production Site Issues
Quickly and flexibly respond to production issues such as yield, equipment utilization rate, and product quality.
-
Cost Reduction
Manage everything from raw materials to sales and customer shipment, including returns after shipment.